The Benefits of Laser Welding Machines for Metal Fabricators
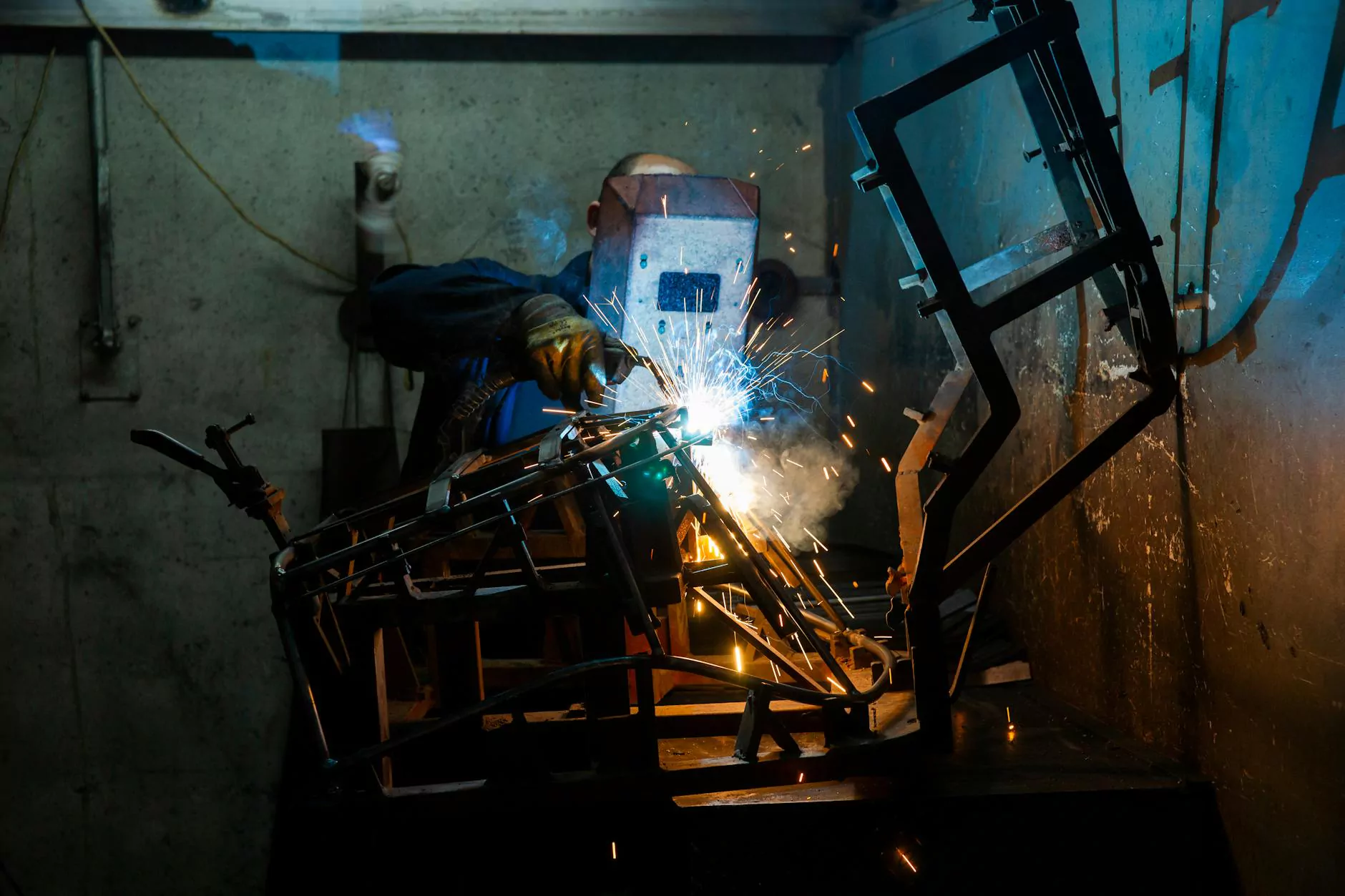
In today's competitive metal fabrication industry, staying ahead of the game requires the use of cutting-edge technology. One such technology that has revolutionized the metal fabrication process is the laser welding machine. With its precision, speed, and versatility, laser welding machines have become an indispensable tool for metal fabricators around the world.
What is a Laser Welding Machine?
A laser welding machine is a high-tech device that uses a focused laser beam to join metals together. Unlike traditional welding methods that rely on heat generated by an electric arc or an open flame, laser welding machines use a concentrated beam of light to melt and fuse the metal surfaces. This process creates a strong and durable bond without significant distortion or damage to the surrounding areas of the material.
The Advantages of Laser Welding Machines
Laser welding machines offer numerous advantages over conventional welding methods, making them the preferred choice for many metal fabricators. Here are some of the key benefits:
Precision and Accuracy
Laser welding machines provide exceptional precision and accuracy, allowing metal fabricators to achieve welds of superior quality. The focused laser beam ensures minimal heat-affected zones, resulting in cleaner and more precise welds. This accuracy is particularly crucial when working with delicate or intricate components, where even minor flaws can compromise the structural integrity of the final product.
Speed and Efficiency
Time is of the essence in the metal fabrication industry, and laser welding machines excel in terms of speed and efficiency. The high-energy laser beams can rapidly heat the metal, allowing for quick fusion and significantly reducing production time. Moreover, laser welding machines often require minimal post-welding finishing work, further speeding up the fabrication process.
Versatility and Flexibility
Unlike traditional welding methods, laser welding machines can be used to join a wide range of metals and alloys. Whether you're working with stainless steel, aluminum, titanium, or even dissimilar materials, a laser welding machine can provide excellent results. Additionally, laser welding machines are suitable for both spot welding and seam welding applications, offering versatility and flexibility to metal fabricators.
Improved Weld Strength
The precise control and concentrated heat input of laser welding machines result in welds with exceptional strength. This is especially crucial for structural components, where the weld's integrity directly impacts the overall strength and durability of the final product. Laser welding machines produce strong, high-quality welds that meet or exceed industry standards, ensuring the longevity of the fabricated metal parts.
Reduced Distortion
Traditional welding methods often lead to distortion or warping of the welded parts due to the excessive heat input. Laser welding machines minimize this issue by delivering a controlled heat input, reducing the chances of distortion. This is particularly beneficial for delicate or precision components that require strict dimensional tolerances.
Enhanced Aesthetics
Laser welding machines offer cosmetic advantages over traditional welding methods. The focused laser beam results in narrow and precise weld seams, providing a cleaner and more visually appealing finished product. This enhanced aesthetic quality is essential for applications where the appearance of the weld is as important as its functionality.
Applications of Laser Welding Machines
The versatility and precision of laser welding machines make them suitable for a wide range of metal fabrication applications. Here are some common uses:
- Automotive Industry: Laser welding machines are widely used in the automotive industry for joining various components, such as body panels, exhaust systems, and suspension parts. The speed and accuracy of laser welding make it a preferred choice for mass production.
- Aerospace Industry: Laser welding machines are essential in the aerospace industry, where high-quality and reliable welds are required to withstand extreme conditions. They are used to fabricate aircraft components, engine parts, and fuel tanks.
- Medical Devices: Laser welding machines play a crucial role in the production of medical devices, such as surgical instruments, implants, and equipment. The ability to create clean and precise welds ensures the safety and effectiveness of these critical tools.
- Electronics: In the electronics industry, laser welding machines are used for joining intricate components on circuit boards and microelectronics. The accuracy and minimal heat input prevent damage to sensitive electronic parts.
- Jewelry: Laser welding machines have become a staple in the jewelry manufacturing industry. Their ability to create strong, visually appealing welds allows for intricate designs and seamless repairs.
These are just a few examples of the vast applications of laser welding machines. With advancements in technology, the possibilities continue to expand, making laser welding a fundamental process in the metal fabrication industry.
Conclusion
Laser welding machines have transformed the way metal fabricators operate, offering unparalleled precision, speed, and versatility. The benefits of laser welding machines extend beyond improved weld quality – they also contribute to increased productivity, cost-effectiveness, and customer satisfaction. As the metal fabrication industry evolves, laser welding machines will undoubtedly remain at the forefront of innovation, enabling businesses like DP Laser to thrive in a competitive market.
Investing in a laser welding machine can be a game-changer for metal fabricators, providing a strategic advantage and opening doors to new opportunities. Embrace the power of laser welding technology today and take your metal fabrication business to new heights!