The Ultimate Guide to Prototype Mold in Metal Fabrication
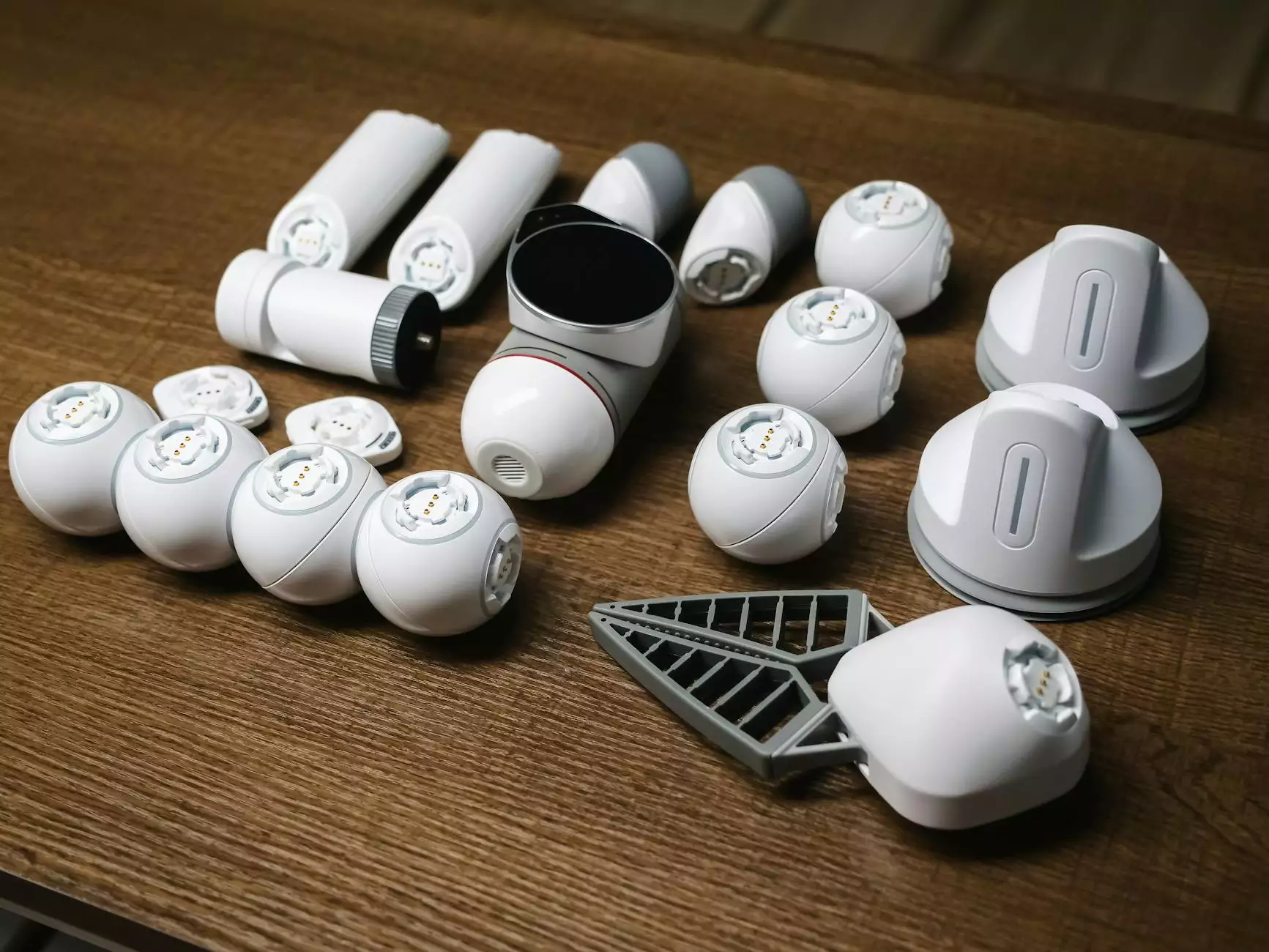
Prototype mold technology is revolutionizing the way industries approach product design and manufacturing. As businesses face greater demand for customized solutions and faster turnaround times, the significance of prototype molds in the realm of metal fabrication cannot be overstated. This article delves into the concept of prototype molds, their applications, benefits, and why they are essential for businesses looking to stay competitive in the ever-evolving market.
What is a Prototype Mold?
A prototype mold is a tool used in the initial phase of product development to create a physical representation of a design idea. These molds are typically produced using materials such as aluminum or steel, and they serve as templates for producing parts or assemblies of the final product. The primary purpose of a prototype mold is to validate design concepts and functionality before committing to larger-scale production.
The Importance of Prototype Molds
In the current fast-paced market, the ability to develop prototypes quickly is crucial for several reasons:
- Faster Time-to-Market: Prototype molds facilitate rapid prototyping, allowing businesses to test ideas quickly and launch products faster.
- Cost Efficiency: Developing a prototype reduces the risk of costly mistakes in later manufacturing stages, helping businesses save money.
- Design Validation: Prototypes enable designers to identify potential issues and refine product designs before full-scale production, ensuring better functionality and user satisfaction.
- Market Testing: Companies can use prototypes to gather customer feedback and make necessary adjustments based on real user experiences.
Applications of Prototype Molds
Prototype molds have a wide array of applications across various industries. Here are some prominent sectors utilizing this technology:
1. Automotive Industry
The automotive sector often requires rigorous testing for new vehicle components. Prototype molds allow manufacturers to create parts that can undergo wear and crash tests, ensuring safety and performance before mass production.
2. Aerospace Industry
In aerospace, precision is critical. Prototype molds are used to fabricate parts that meet strict regulatory standards while allowing engineers to fine-tune designs for better aerodynamics and fuel efficiency.
3. Consumer Electronics
The rapid evolution of technology requires companies to innovate continuously. Using prototype molds, manufacturers can create compact and efficient designs for electronic gadgets, ensuring functionality and style.
4. Medical Devices
In the medical field, prototypes can be the difference between life and death. Prototype molds help create devices that need to meet stringent health standards while providing functionality to healthcare providers.
Benefits of Using Prototype Molds
The investment in prototype molds offers numerous benefits for metal fabricators and businesses alike:
Rapid Prototyping
With advancements in technology, prototype molds can be produced rapidly. This allows businesses to iterate on designs quickly, enabling faster development cycles.
Improved Design Accuracy
Utilizing prototype molds results in more accurate representations of end products. This accuracy ensures that design specifications are met, reducing the likelihood of costly modifications later on.
Enhanced Collaboration
Prototyping fosters collaboration among teams. Designers, engineers, and manufacturers can all work together to refine a product before it hits the market, ensuring all perspectives are considered.
Quality Assurance
Prototype molds undergo rigorous testing and refinement processes, helping ensure that final products meet quality standards. This approach reduces returns and increases customer satisfaction.
Choosing the Right Prototype Mold Provider
When selecting a partner for your prototype mold needs, certain criteria should be assessed:
- Experience: Look for a provider with a proven track record in producing high-quality molds in your industry.
- Technical Capability: Ensure they use advanced technologies like CNC machining and 3D printing for creating precise molds.
- Customization: Choose a mold fabricator that offers tailored solutions to meet your specific design and material requirements.
- Customer Support: Reliable after-sales support is vital to address any issues that may arise during the prototyping and production process.
The Process of Creating a Prototype Mold
The journey of creating a prototype mold involves several key steps, each critical to ensuring the success of the final product:
Step 1: Design Review
The first step involves a thorough review of the design specifications. Engineers and designers collaborate to finalize the mold configuration and the materials required.
Step 2: CAD Modeling
Using advanced computer-aided design (CAD) software, a detailed 3D model of the prototype is created. This model serves as the basis for the mold fabrication process.
Step 3: Mold Fabrication
Once the design is complete, the mold is fabricated using CNC machining, EDM (Electrical Discharge Machining), or 3D printing techniques, depending on precision needs and material properties.
Step 4: Testing and Validation
The prototype is produced using the mold, which is then subjected to rigorous testing to validate its functionality and design accuracy.
Step 5: Iteration and Refinement
Based on testing results, further refinements may be made to the mold or design to ensure that the final product meets all necessary requirements.
The Future of Prototype Molds in Metal Fabrication
As technology continues to advance, the future of prototype molds looks promising:
Advancements in Materials
New materials are being developed that offer improved durability and heat resistance, which can enhance the quality of molds and the products they produce.
Integration of 3D Printing
3D printing technology is becoming increasingly integrated into the prototyping process, allowing for more flexible design changes and reduced lead times.
Smart Manufacturing
With the rise of IoT (Internet of Things), smart manufacturing will enable more data-driven decision-making in the prototyping phase, leading to better efficiency and productivity.
Conclusion
In conclusion, prototype molds play a pivotal role in the metal fabrication industry. They not only facilitate faster product development but also ensure accuracy and cost-effectiveness throughout the manufacturing process. By choosing the right partner, such as the experts at deepmould.net, businesses can leverage these molds to create innovative products that resonate in the competitive marketplace. Investing in prototype molds is not just a step toward efficiency; it’s a leap into the future of manufacturing excellence.
Get Started with Prototype Molds Today!
If you're ready to take your product development to the next level, visit deepmould.net for expert assistance with your prototype mold needs. Our team of experienced metal fabricators is here to ensure you achieve the highest quality results at every stage of production.